
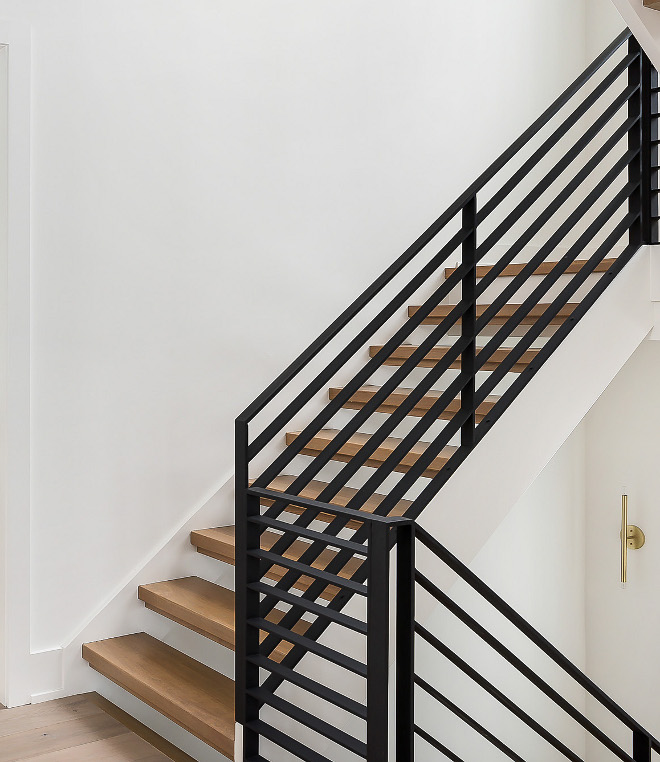
For all intents and purposes, “wrought iron” is used more as a term for a style than it is for a building material. This usually means ornamental scrollwork, twists, baskets, or knuckles on the balusters. What most people are actually looking for when they specify “wrought iron railings” is a particular look. What Does This Mean for Homeowners Looking for Wrought Iron?

Over a century later, it’s rare to find even an old piece of iron, and getting ahold of fresh iron stock is expensive and nearly impossible unless you’re doing a historical restoration. When the Bessemer process that could turn out steel economically was invented in 1853, steel rapidly replaced iron so that by the turn of the twentieth century, fewer than 50 years later, iron wasn’t used anywhere. The inability to distribute force evenly applies to iron under load, and in iron’s heyday as a structural material it often failed, sometimes with catastrophic consequences.
#BLACK STEEL RAILING CRACK#
This can cause it to crack while it’s being worked, with a tell-tale ping that is a welder’s nightmare. Because the material has an uneven density it also means that forces aren’t distributed evenly through it when it is heated. Wrought iron is hard to work with because its unevenly dense due to an unevenly distributed amount of carbon, which forms visible flakes and nodules.
#BLACK STEEL RAILING UPDATE#
The knowledge needed to weld iron is also uncommon the only reason that I know it is that the military is slow to update its training and technical manuals. This is in comparison to steel, where welding is mostly just making sure the measurements are correct and then going ahead with the welding. Only once you are fairly certain that it is evenly heated to just shy of melting can you begin welding, and intermittently you have to take a hammer and hit it to release any stress that may be building up in the metal as you weld. You use a torch to preheat the metal and getting it evenly heated is a challenge, to say the least. The standard procedure is to evenly preheat the metal before welding, and this takes some time. Wrought iron is an unpleasant material to work with, especially for welders. This became a massive headache for anyone in the company who worked with their hands. She would settle for nothing less than the real deal, and because it was a large home and such a large project for the company, the owners were unwilling to turn her away. This became an issue for one customer who wanted genuine wrought iron railings for her dream home going up by a lake. They were built from mild steel, a superior material and one that is far easier to work with than wrought iron. However, these weren’t wrought iron railings. When he was done, we’d have black steel rail panels that assembled into wrought iron-look railings that could’ve come straight from Victorian London. I would carefully cut each piece, bend it to shape, weld the pieces together, and then carry them over to the painter who would give them a couple of coats of paint.

Our bread and butter, though, was ornamental steel railings for staircases, balconies, and lofts. We built everything from aluminum boat guardrails to ultra-modern stainless steel lighting fixtures. One of the jobs I got shortly after the military was as a welder in a custom metalworking shop.
